Case study grabber
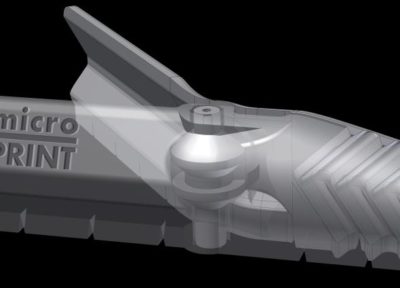
Cost reduction by saving assembling – Functional module built at-once by Micro Laser Sintering
Grabbers or manipulators are used in numerous branches from medical technology to aerospace. Using conventional technologies such a grabber has to be assembled at least of four single pieces. The smaller the parts become, the more difficult the secure assembling of the tiny components is.
Functional modules and mechanisms made of metal can be manufactured easily with Micro Laser Sintering. The functionality is being created directly during the building process. Afterwards no additional assembling is necessary, so the grabber can be used immediately afterwards. The Micro Laser Sintering systems provided by
3D MicroPrint GmbH introduce new possibilities to the customer in terms of innovative functional integration and miniaturization of their products. The absence of joints between the individual parts also increases the robustness of the construction.
The featured parts were manufactured with a DMP50 GP Micro Laser Sintering system developed by 3D MicroPrint GmbH.